HEY, WE ARE BONPRIX!
About Us
Fashion is our passion. With our range of products, we want to inspire and excite our customers every day. Diverse. Personal. Responsible.
Newsroom
News News News!
We never stand still. Current corporate announcements, the latest fashion trends, or our Fashion Report – there is always something to discover.
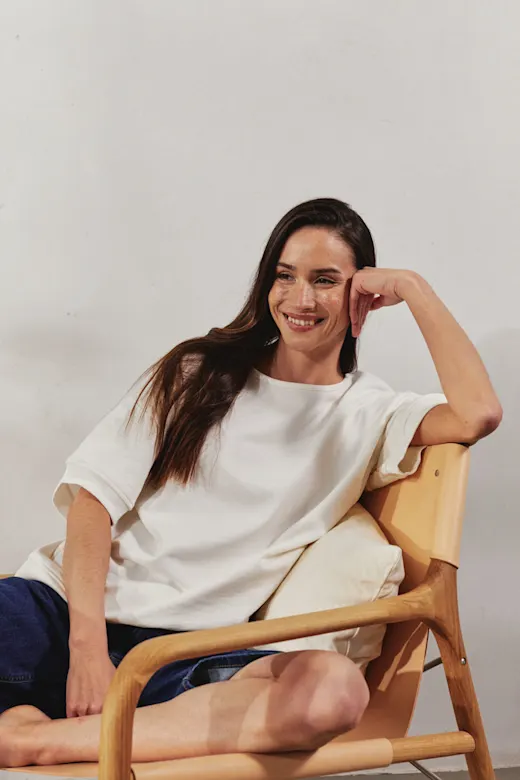
Responsibility
We take responsibility. The use of more sustainable materials, the development of circular products, and transparency for our customers are our focus.
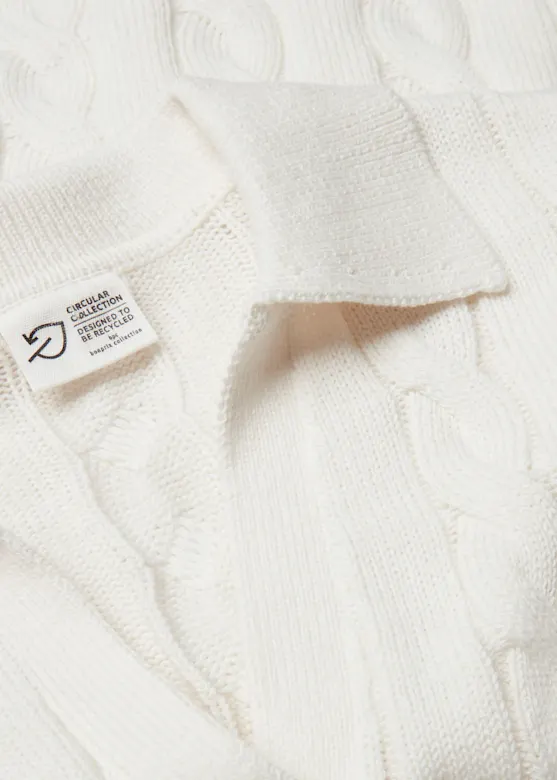
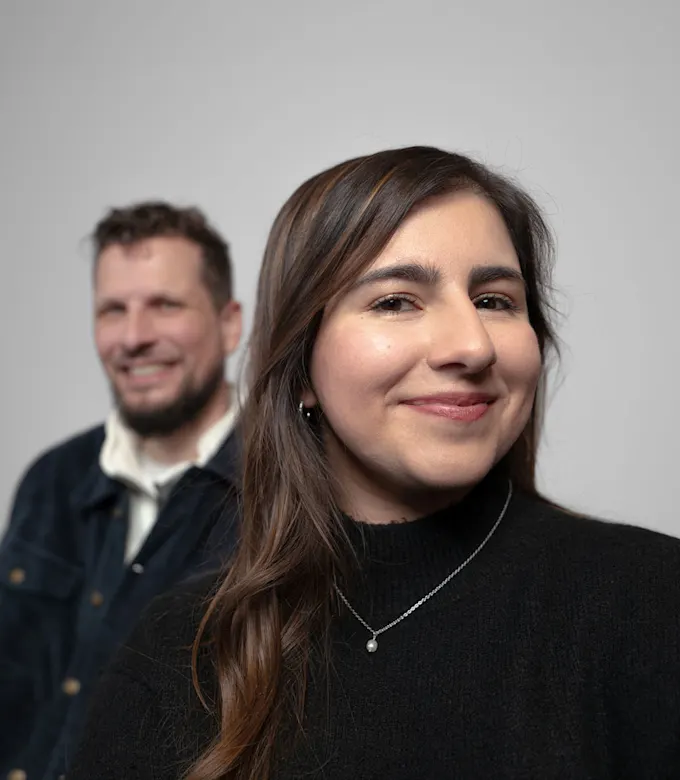